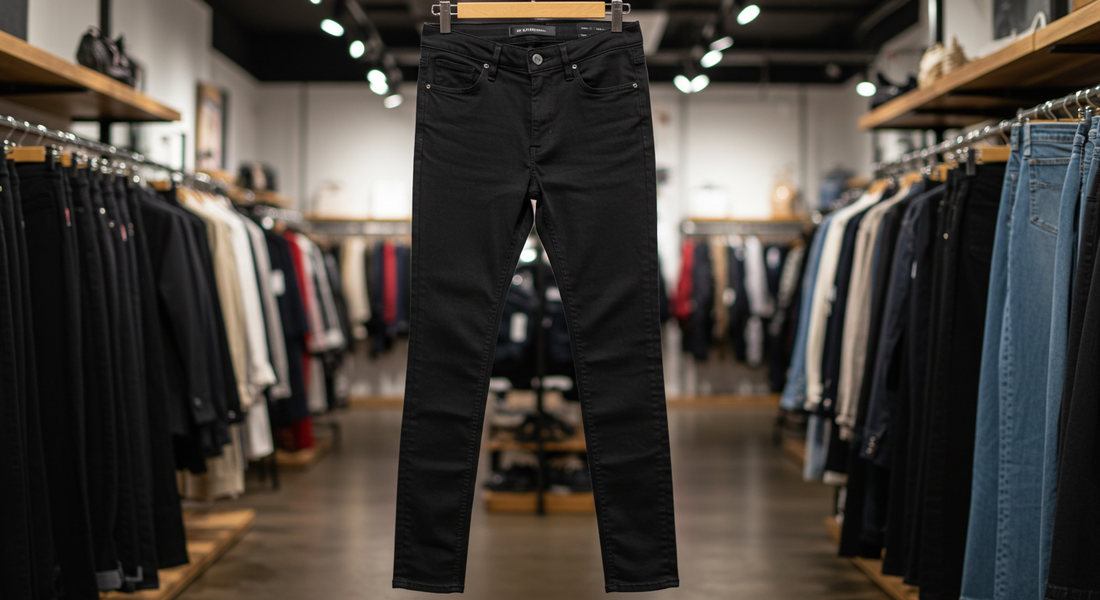
The Ultimate Guide to Jeans Manufacturing for Modern Retailers
The global jeans market reached $56.2 billion in 2023, making jeans manufacturing one of the most crucial segments in the fashion industry. For modern retailers, understanding the intricacies of this manufacturing process has become more important than ever.
The landscape of jeans manufacturing has transformed significantly with technological advancements and sustainable practices. As the denim future shifts toward eco-friendly production and the new denim project initiatives gain momentum, retailers must adapt to stay competitive.
This comprehensive guide explores every aspect of modern jeans manufacturing, from essential production processes and raw material selection to quality control systems. Whether you're an established retailer or new to the industry, you'll find practical insights to optimize your manufacturing operations.
Understanding Modern Jeans Manufacturing
Modern jeans manufacturing has evolved into a sophisticated process that combines traditional craftsmanship with cutting-edge technology. The industry produces approximately 15 billion meters of denim annually, with Asia-Pacific nations including China, Turkey, Pakistan, and Bangladesh accounting for half of the global output.
Key Components of Production
The foundation of jeans production lies in its core components, starting with fiber selection and preparation. Today's denim has moved beyond traditional 100% cotton composition, incorporating innovative blends and sustainable materials. Modern manufacturers focus on durability requirements, ensuring jeans can withstand a minimum of 30 home laundries while maintaining quality standards.
Technology in Manufacturing
The technological landscape of jeans production has witnessed significant advancement. Modern manufacturing facilities employ:
- Computer-aided design (CAD) for precise pattern making
- Automated cutting systems for material optimization
- Advanced dyeing technologies using up to 70% fewer chemicals
- Laser finishing and digital printing capabilities
The integration of nitrogen-based dyeing technology has revolutionized the coloring process, allowing deeper pigment penetration and more gradual fading patterns. Additionally, water-saving innovations in finishing processes have become crucial, with technologies like ozone washing and laser treatments reducing environmental impact while maintaining quality.
Quality Standards and Specifications
Quality control in modern jeans manufacturing involves rigorous testing and inspection protocols. Tensile strength measurement plays a crucial role, as jeans undergo frequent stretching and movement. The industry follows specific standards for:
- Color fastness testing to ensure dye retention
- Weave and construction analysis for durability
- Material health verification, requiring minimum 98% cellulose fibers
- Traceability documentation for all production elements
Modern quality assurance systems incorporate AI and data-driven technologies to optimize production processes and reduce waste. These systems ensure that each component meets stringent requirements while maintaining efficiency in large-scale production.
The industry's commitment to innovation extends to sustainability initiatives, with manufacturers implementing closed-loop manufacturing processes where old denim can be recycled into new fabric. This approach, combined with advanced recycling technologies, represents the denim future's direction toward more sustainable production methods.
Essential Manufacturing Processes
Production excellence in jeans manufacturing relies on precise execution of three critical processes: cutting, sewing, and finishing. Each pair of jeans requires approximately 1.5 meters of regular denim or 2.5 meters of selvedge denim, along with several hundred meters of thread in various thicknesses.
Cutting and Sewing Techniques
The journey begins with precise pattern cutting, where computer-aided design systems guide automated cutting machines through multiple layers of denim simultaneously. These machines use either lasers or sharp blades to ensure consistency across all sizes.
Modern sewing techniques employ specialized industrial machines designed specifically for heavy fabrics. A standard five-pocket jean consists of roughly 20 separate pieces. Key sewing elements include:
- Chain stitching for seam flexibility and strength
- Lock stitching for permanent, durable seams
- Flat-felled seams for enhanced durability
Washing and Finishing Methods
The washing process transforms raw denim into the comfortable, worn-in jeans consumers prefer. Modern facilities employ various techniques:
Stonewashing remains a foundational process, using pumice stones to create a naturally worn appearance. However, innovative methods have emerged, including:
- Enzyme washing for softer fabric and subtle fading
- Ozone treatment for eco-friendly color modification
- Laser distressing for precise wear patterns
The finishing process typically involves multiple stages, with jeans going through desizing, washing, and softening treatments. Advanced techniques like ozone fading can reduce water usage by approximately 2 liters per linear meter of denim.
Quality Control Points
Quality assurance occurs throughout the manufacturing process, with specific checkpoints for:
-
Pre-production Testing
- Fabric shrinkage assessment
- Color fastness verification
- Seam strength evaluation
Each garment undergoes rigorous inspection for inconsistencies in color, stitching quality, and overall fabric integrity. Performance testing includes abrasion resistance checks and tear strength analysis to ensure durability standards are met.
Modern quality control incorporates both visual inspections and automated testing systems. Manufacturers typically conduct shrinkage tests using 1×1 meter fabric squares to adjust patterns accordingly, ensuring consistent sizing across production runs.
Raw Materials and Supplier Management
The foundation of successful jeans manufacturing lies in selecting premium raw materials and building strong supplier partnerships. With cotton comprising 91% of denim products, understanding material quality and supplier management becomes crucial for modern retailers.
Selecting Quality Denim Fabric
Quality denim selection starts with evaluating key physical properties. The fabric's weight, typically ranging from 9 to 14 ounces per square yard, determines its durability and application. Modern manufacturers assess:
- Tensile Strength: Measures maximum load capacity before breaking
- Color Fastness: Evaluates resistance to fading during washing
- Weave Construction: Analyzes 3×1 or 2×1 twill patterns for strength
The industry's shift toward sustainable materials has introduced new quality parameters. Manufacturers now source cotton from farmers who reduce water and chemical usage while increasing yields. This approach aligns with the denim future while maintaining fabric integrity.
Managing Supplier Relationships
Effective supplier management requires a strategic approach to partnership building. Clear communication channels and regular face-to-face meetings help prevent confusion and streamline operations. Key aspects include:
- Establishing transparent performance metrics
- Maintaining consistent payment schedules
- Developing long-term collaborative programs
Supplier diversification has become increasingly important, with China's share of global denim exports declining from 60% to 50%, while countries like Pakistan, Turkey, and Egypt expand their market presence.
Cost Control Strategies
Cost optimization in denim manufacturing follows a structured breakdown: 50% for raw materials, 24% for factory costs, and 8% for logistics. Successful cost control strategies include:
Material Innovation
- Utilizing sustainable materials that offer long-term savings
- Implementing recycled denim programs
- Exploring alternative fibers like hemp and bamboo
Supplier Partnerships Modern manufacturers negotiate contracts reflecting volume discounts and long-term savings. This approach has proven particularly effective when working with suppliers specializing in sustainable fabrics.
The integration of technology-based interventions, such as Radio Frequency Identification (RFID), has enhanced inventory management while reducing waste and overordering. These innovations help maintain quality standards while optimizing material usage and controlling costs throughout the supply chain.
Production Planning and Control
Effective production planning serves as the cornerstone of successful jeans manufacturing, requiring precise coordination between different manufacturing phases. Modern manufacturers are shifting toward data-driven approaches, using real-time analytics to optimize production schedules and monitor machine performance.
Capacity Planning
Manufacturing capacity planning helps determine the exact production capacity needed to meet market demand. Modern denim facilities consider several crucial factors:
- Available workforce hours and shifts
- Equipment utilization rates
- Raw material availability
- Production line efficiency
- Quality control requirements
A well-structured capacity plan can reduce manufacturing lead times by up to 40% while maintaining product quality standards. This approach becomes particularly critical in denim production, where both make time and wash time occur in different facilities.
Timeline Management
Production timelines in jeans manufacturing follow a structured sequence, typically spanning 8-10 weeks from initial cutting to final shipping. The process requires careful orchestration of multiple stages:
- Post-show order processing (1 week)
- Material procurement (4-8 weeks)
- Production initiation (4-6 weeks)
- Quality inspection and shipping prep (2 weeks)
Effective timeline management becomes especially crucial when dealing with specialized denim treatments, as replanning within wash houses or sewing factories can significantly impact lead times.
Resource Allocation
Resource allocation in modern jeans manufacturing combines traditional expertise with technological innovation. The industry now employs predictive maintenance algorithms to ensure machines operate at peak efficiency, minimizing downtime and maximizing productivity.
Workforce Management Modern facilities focus on strategic workforce deployment, ensuring skilled operators are available for specialized processes like indigo dyeing and finishing. Training programs have become integral, with companies investing in regular skill development sessions to maintain production quality.
Equipment Utilization Smart resource allocation extends to equipment usage, where manufacturers implement automated systems for tracking machine performance. This approach has shown to improve overall equipment effectiveness by reducing idle time and optimizing maintenance schedules.
The integration of data analytics in resource planning has transformed how manufacturers approach capacity utilization. By leveraging real-time production data, facilities can now make informed decisions about resource deployment, leading to more efficient operations and reduced waste in the manufacturing process.